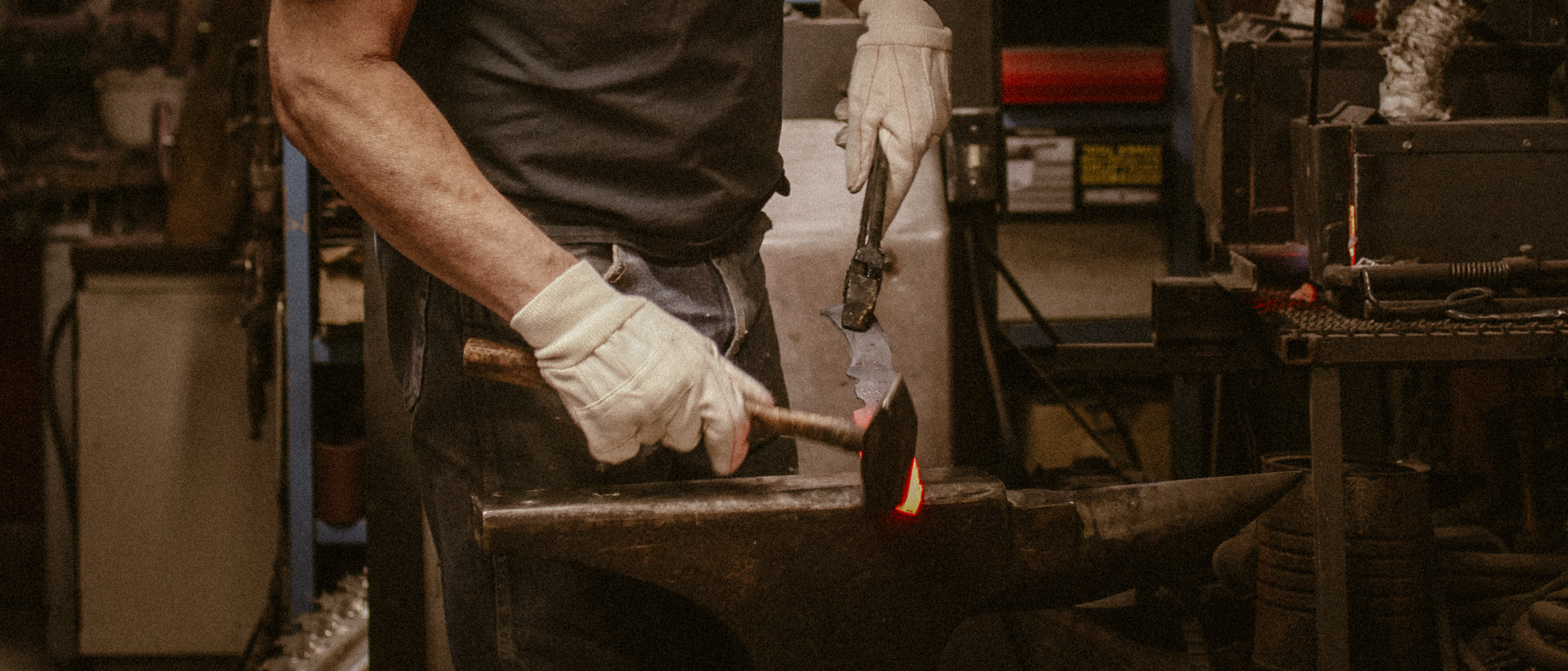
QUALITY HAND MADE
From the mountains of North Idaho. Saw steel is recycled from the local wood mills and reborn. Blades are forged, shaped, reground and heat treated, handles are fitted and a custom leather sheath is made.
About C Thomas Knives
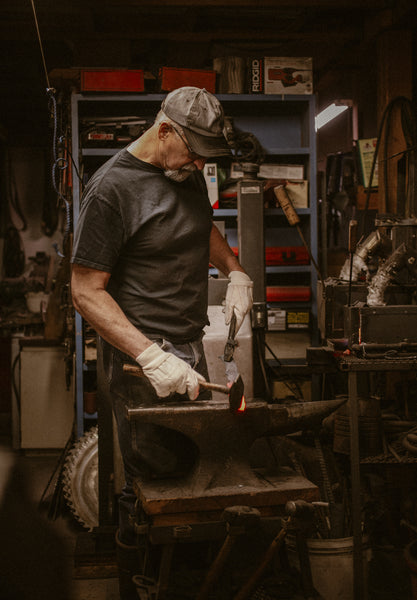
My hands have always been busy. In the military I was a hospital corpsman suturing lacerations and administering medications. Out of the service I worked in a hospital laboratory and ran a seasonal taco stand. Later I operated some heavy equipment and then determined to build my own house with a large shop along side. I have always kept busy with my hands. It’s been said that, “blessed is the man that finds enjoyment in his toil“. That would describe me best.
I like to think I build a decent knife, having acquired knowledge and experience from makers like Allen West and Ray Rantanen. An original buckskinner, knife maker, muzzle loader gunsmith, Allen taught me the basics: heat treating, tempering and general knife construction. He gave me my first handmade knife made of elk tine and 01 tool steel. Previously I never owned a knife that truly worked well, my experience was with production knives that either would not hold an edge or were too hard to sharpen, especially in the field. My new “handmade” knife was different. It had character, cut excellent and (when needed) sharpened easily. Making a quality knife is what started many hours in the shop learning from Allen’s 30 years of experience. Later I met Master Blacksmith-Bladesmith Ray Rantanen. Ray is self taught with first hand experience, having pleased thousands of customers, Ray taught me some finer points of knife making, Damascus steel and leather work. These men and others, caused my enthusiasm for the craft to increase dramatically.
After making a few knives for my friends and family, I began receiving referrals and before I knew it, I was attending a local gun show and sold a few, at a local craft show a few more were bought. Customers soon returned and acquired a knife or two for family members as gifts. It appeared there where others that had appreciation for my knives.
To sum it up, that’s what got me started and now I can’t stop! Thanks to those who had the patience to show me the tricks of the trade.
Knife Making Methods and Materials
Originally starting with a 3 ft. circular saw blade or double cut band saw blade I would rough out shapes with a chop saw. Now I use a plasma cutter, only the largest heaviest blades and all Damascus blades do I forge into shape. Medium and smaller blades the stock is removed by slack belt grinding on a soft platen, this brings about the convex edge.
Note: Most thinner blades are reground from 8670 (similar to L6 tool steel) German and Swedish industrial saw steel, recycled from the wood mills of North Idaho. Forged blades are from 01, L2, 8670, 5160 tool or spring steels or a combination thereof for Damascus.
While most industrial saw steel is good or great steel for making knives I think the smaller blades with carbide tips for handheld saws and table saws is questionable steel.
For those who are interested in the chemistry of the saw steels I use, here is the break down from a very expensive spectroscopy machine.
Carbon |
Manganese |
Silicon |
Chrom |
Nickel |
Moly |
Vanadium |
|
2 ft. circular (8670) | .677 |
.495 |
.298 |
.40 |
.85 |
.074 |
.016 |
2.5 ft. circular (8670) | .675 |
.463 |
.233 |
.43 |
.758 |
.109 |
– |
5 ft. circular (80CrV2) | .80 |
.56 |
.275 |
.53 |
.034 |
– |
.158 |
12 in. bandsaw (15N20) | .742 |
.42 |
.232 |
.134 |
2.00 |
.01 |
– |
Heat Treating
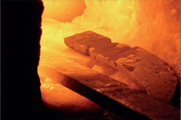
Larger blades are brought to just over critical temp [1550 o F]. In a reducing atmosphere forge and quenched at 125 F in vegetable oil. Depending on the blade it is either edge quenched or the whole blade is submerged.
Small to medium sized blades are brought to just over critical temp with a oxygen/acetelyne torch with a carburizing flame and edged quenched and then left to air cool on a towel. The blades depending on their use, are tempered at 350-550 F. For 2 hours in a convection oven. By this procedure the resulting Rockwell hardness is 58-60 hc at 350 F.
Finger Guards & Bolsters

I notch the bottom of the tang of the knife for a stop and also grind fine grooves in the tang where the guard is to be silver soldered on, making a very complete bond for the solder. Bolsters are pinned and epoxied. My favorite material to use is copper. It is hard to work with but I think the added effort is worth it. I also use brass and mild steel.
Handles

With wood in most cases I vacuum stabilize with a heat cured resin. On oily hardwood I prep the wood with alcohol or acetone before I hand rub a Profin finish 4-8 coats depending on the wood. Bone and antler, if porous, is sealed with cyanoacrylate {super glue}. Then all handles are hand waxed with Collinite carnauba wax. Kitchen knife steel is coated with coconut oil. Though I always strive to use the best materials available there are sometimes imperfections in natural handle material that are outside my control.
Sheaths
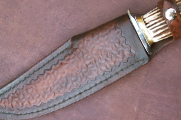
I mostly use vegetable tanned 7-12oz shoulder leather hand sewn with a welt. Most sheaths are wet molded to fit the knife. After tooling , dying and drying they are buffed and burnished, then, 2 coats of Tandy’s Tan Kote are applied. For custom sheaths initials or a name can be added at little or no cost. Also horizontal carry sheaths can be made upon request for most small and medium sized knives.
Etching
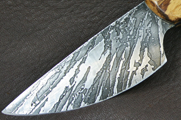
Adds uniqueness to the knife. The etching process is a combination of a strong alkali or acid solution and heat, the depth of the etch is a shallow 1 thousands to a deeper 4 thousands. Varying designs on the blade come forth which I can rarely duplicate so each knife is unique . After the etch the blade is neutralized with vinegar or ammonia. On deeper etches gun bluing is applied for contrast and then hand sanded with a worn 900 grit belt. The etch truly makes for a one of a kind knife. When I am at a show many people assume that some of my etched knives are Damascus steel. Though I do make my own Damascus steel I point out the difference between the two. Sometimes it is hard to tell the difference because a few of the etched blades look a lot like cable Damascus.
Available Knives
-
7.5 inch Custom Chef, Ponderosa pine
Regular price $450.00 USDRegular priceUnit price / per -
Custom 5.5 inch Camp/chef, African blackwood
Regular price $450.00 USDRegular priceUnit price / per -
Fancy Drop point Hunting Knife, box elder
Regular price $675.00 USDRegular priceUnit price / per -
6.5 inch Camp/Chef knife, Mexican Ebony
Regular price $650.00 USDRegular priceUnit price / per